(Québec) « Le premier patient qu’on va traiter ne sait pas encore qu’il a le cancer. Probablement qu’il est chez lui, qu’il ressent de la douleur et se dit que ça va passer… »
Le Dr Benoît Guay répare depuis des années les dégâts causés par les tumeurs de la bouche. Le chirurgien maxillo-facial, qui œuvre au CHU de Québec-Université Laval (CHU), sait trop bien comment elles peuvent sournoisement éroder la mâchoire et la scier en deux.
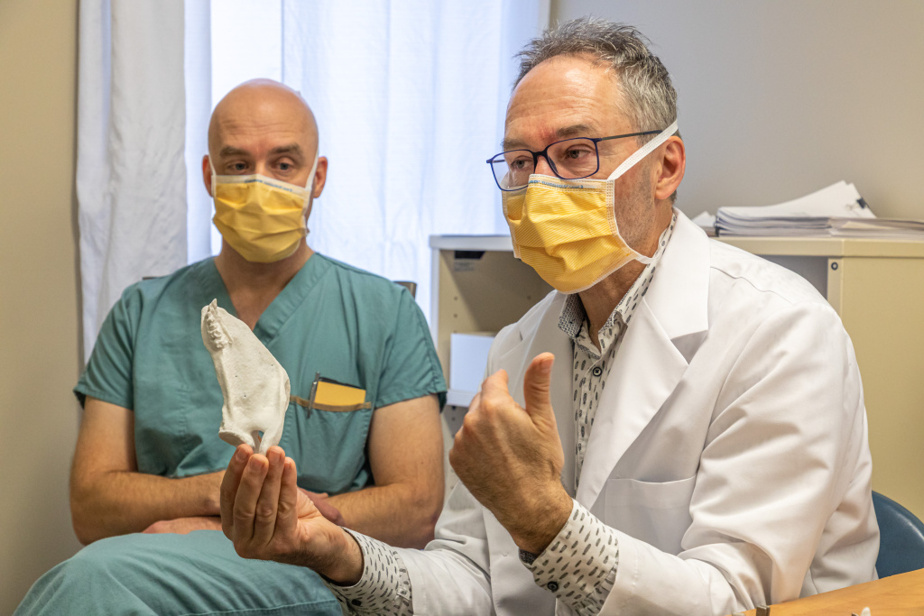
PHOTO PAUL DIONNE, COLLABORATION SPÉCIALE
Le Dr Benoît Guay, chirurgien maxillo-facial, et le Dr Gaston Bernier, dentiste-oncologue, ont piloté le volet médical du projet d’implants au CHU de Québec-Université Laval.
En février, une nouvelle arme lui permettra d’atténuer les souffrances de certains patients : le tout premier implant médical fabriqué au Canada avec une imprimante 3D.
Cette technologie – aussi appelée fabrication additive – révolutionne la médecine en permettant de produire – une à la fois – des prothèses sur mesure, parfaitement adaptées à l’anatomie de chaque patient.
Les nouveaux implants de mâchoire seront modélisés au CHU à partir de radiographies. Ils seront ensuite imprimés au Laboratoire de reconstruction anatomique 3D d’Investissement Québec – Centre de recherche industrielle du Québec (CRIQ), une société d’État qui aide les entreprises québécoises à adopter les nouvelles technologies.
C’est la première fois que Santé Canada autorise une organisation canadienne à commercialiser un implant médical imprimé en 3D.
Le CHU et le CRIQ ont réalisé cette première après quatre ans d’efforts.
Santé Canada leur permet d’approvisionner tous les hôpitaux canadiens qui en feront la demande, à condition de respecter certains standards de livraison.
« On vient d’ouvrir une voie qui n’existait pas »
L’autorisation obtenue concerne une mince barre de titane, conçue pour reconstruire la mâchoire inférieure en y fixant un nouveau segment d’os.
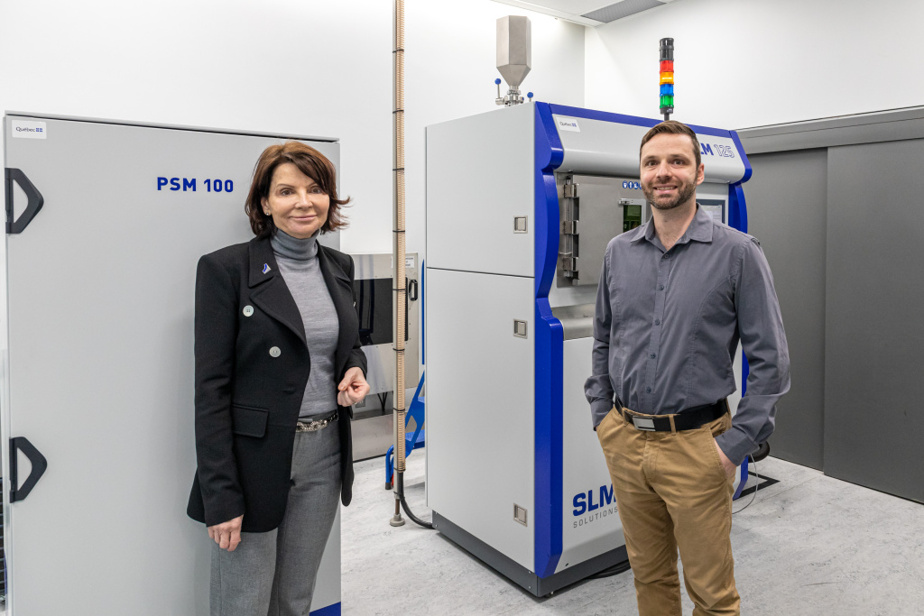
PHOTO PAUL DIONNE, COLLABORATION SPÉCIALE
Le CRIQ possède deux imprimantes médicales 3D et une imprimante industrielle distincte, pour éviter toute contamination. Sur la photo, Lyne Dubois, vice-présidente du CRIQ, et l’ingénieur mécanique Olivier Marcotte.
Et ce n’est qu’un début, prédit la vice-présidente du CRIQ, Lyne Dubois, qui envisage d’autres collaborations et la fabrication d’autres implants. « On vient d’ouvrir aux entrepreneurs québécois une voie qui n’existait pas », se réjouit-elle (voir onglet suivant).
L’ingénieur mécanique Olivier Marcotte, qui travaille aussi au CRIQ, abonde dans le même sens. « Peu importe la forme à produire, on peut utiliser le même appareil. C’est un gros avantage », précise-t-il.
-
IMAGE FOURNIE PAR LE CENTRE DE RECHERCHE DU CHU DE QUÉBEC-UNIVERSITÉ LAVAL
Voici comment un logiciel transforme un simple CT-scan (tomodensitométrie) en modèle 3D. Les scans balayent une partie du corps, millimètre par millimètre. Un implant imprimé en 3D est reconstruit exactement de la même manière, couche par couche.
-
IMAGE FOURNIE PAR LE CENTRE DE RECHERCHE DU CHU DE QUÉBEC-UNIVERSITÉ LAVAL
Des guides de coupe – qui sont eux aussi imprimés sur mesure – permettent aux chirurgiens de mieux réussir leurs reconstructions, en éliminant les tâtonnements. Le guide s’adapte parfaitement à l’anatomie de chaque individu.
-
IMAGE FOURNIE PAR LE CENTRE DE RECHERCHE DU CHU DE QUÉBEC-UNIVERSITÉ LAVAL
Les barres de titane imprimées par le CRIQ servent à fixer l’os sculpté par le chirurgien à ce qui reste de la mâchoire.
Le Dr Gaston Bernier, chef médical du Service de médecine dentaire en oncologie au CHU, compte déjà concevoir d’autres types d’implants. « On pourra fabriquer des solutions inédites en quelques jours. Une radiographie et un logiciel de transformation suffisent », dit-il.
Inutile de passer par des multinationales ! On a tous les experts et toute la matière première au Québec. On peut très bien développer une capacité de production autonome à coût raisonnable.
Le Dr Gaston Bernier, chef médical du Service de médecine dentaire en oncologie au CHU de Québec-Université Laval
Le dentiste-oncologue a bon espoir de pouvoir obtenir – au cas par cas – la permission spéciale d’implanter des prothèses destinées à la mâchoire supérieure, au crâne, à la colonne vertébrale, etc.
Reconstruction plus précise et plus rapide
Reconstruire une mâchoire inférieure requiert actuellement une dizaine d’heures. Les chirurgiens doivent prélever un morceau d’os de jambe et le sculpter soigneusement pour remplacer la zone grugée par le cancer.
Les barres métalliques utilisées pour relier le tout doivent être courbées avec minutie, puis stérilisées, en pleine intervention. Ce qui peut prendre une heure.
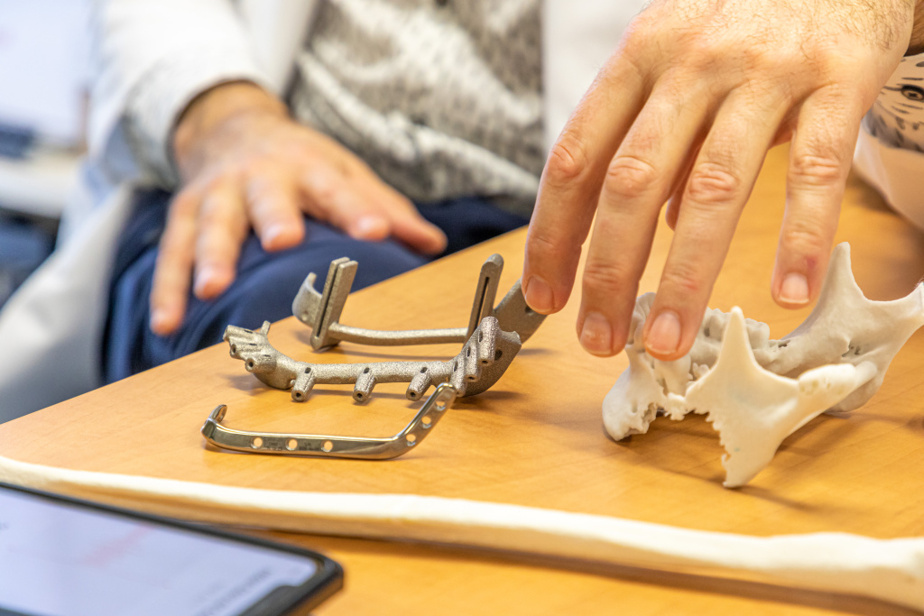
PHOTO PAUL DIONNE, COLLABORATION SPÉCIALE
Le prix des barres mandibulaires imprimées sur mesure devrait fortement chuter lorsqu’elles seront produites en plus grand nombre.
Les nouveaux implants du CRIQ arriveront déjà parfaitement moulés et stérilisés.
En épargnant une heure de chirurgie, on épargnera une heure de saignements et on réduira la souffrance, les risques d’infections et les complications. On aura moins besoin de ramener des patients au bloc opératoire, d’occuper des lits et des ressources.
Le Dr Benoît Guay, chirurgien maxillo-facial au CHU de Québec-Université Laval
À l’heure actuelle, plus de 10 % des patients doivent être réopérés dès la première année.
« Dans certains cas, les plaques actuelles fracturaient et pouvaient même transpercer la peau, expose le Dr Guay. Tout se mettait à bouger, le patient ne pouvait plus manger. »
N’ayant plus à être pliés, les nouveaux implants sont faits d’un alliage plus résistant. En plus d’épouser le contour de l’os à la perfection, ils sont donc plus petits. « Le résultat s’avérera beaucoup plus esthétique », affirme le chirurgien.
Les implants du CRIQ sont accompagnés de guides de coupe et de vissage, eux aussi adaptés à l’anatomie de chaque patient, précise-t-il. « Parce que si la barre ne se trouve pas placée exactement à la bonne place, les dents fermeront mal et manger sera difficile. »
Si tout va bien, une douzaine de patients québécois bénéficieront de cette innovation en 2022, et par la suite, plusieurs dizaines.
Des couches aussi minces que du papier
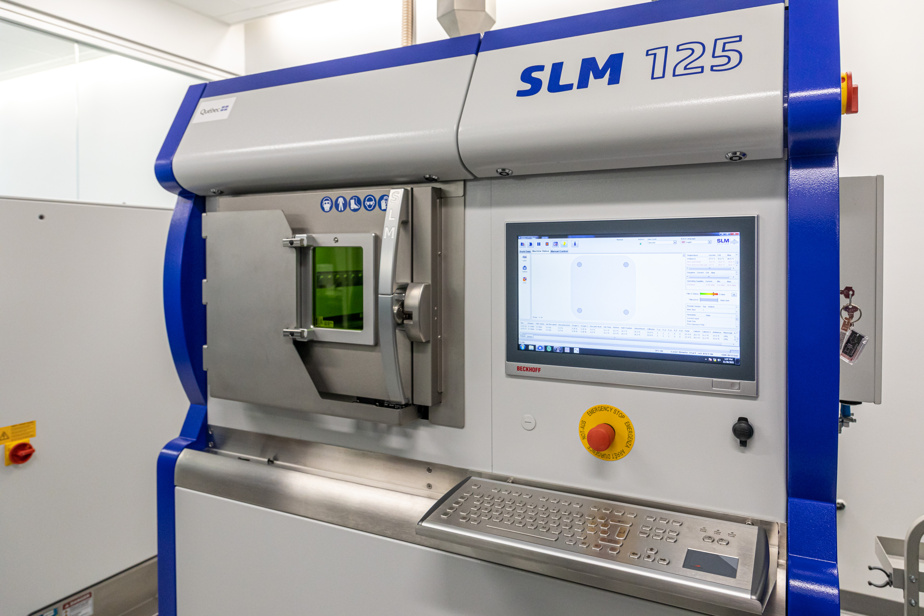
PHOTO PAUL DIONNE, COLLABORATION SPÉCIALE
Imprimante médicale du CRIQ
Les imprimantes médicales du CRIQ sont plus hautes qu’un humain, mais la chambre interne qui abrite leurs créations fait moins d’un mètre carré. Y imprimer une barre mandibulaire requiert une dizaine d’heures. Des couches de poudre métallique aussi fines qu’une feuille de papier s’additionnent, déposées une à une par la tête de l’imprimante. Derrière une vitre verte, qui coupe les longueurs d’onde, des traits lumineux apparaissent par intermittence. Ils sont provoqués par un faisceau laser guidé par un logiciel. Le laser fait fondre les strates de poudre aux endroits souhaités afin de les fusionner.
Le cancer de la bouche
On diagnostique environ 450 nouveaux cancers de la bouche chaque année au Québec. Environ 70 d’entre eux érodent la mâchoire inférieure et sont guérissables (donc admissibles à recevoir un implant chirurgical). « Souvent, quand les patients arrivent dans notre bureau, ils sont au bout. Ça fait longtemps qu’ils ont de la douleur, qu’ils ont du mal à manger, qu’ils ne dorment pas », constate le chirurgien Benoît Guay, qui presse donc les gens de consulter sans tarder si des symptômes inhabituels perdurent, quels qu’ils soient. L’alcool, le tabac et le virus du papillome humain (VPH) – qui touche surtout des gens plus fortunés, contrairement aux deux premiers facteurs – augmentent le risque.
8 millions
Somme investie pour mettre au point et faire homologuer le nouvel implant mandibulaire du CHU et du CRIQ
0,5 à 1 million
Coût des imprimantes 3D du CRIQ
15 000 à 20 000 $
Prix approximatif des barres de reconstruction imprimées la première année (le prix unitaire devrait chuter en fonction du volume)
Des ponts aux avions
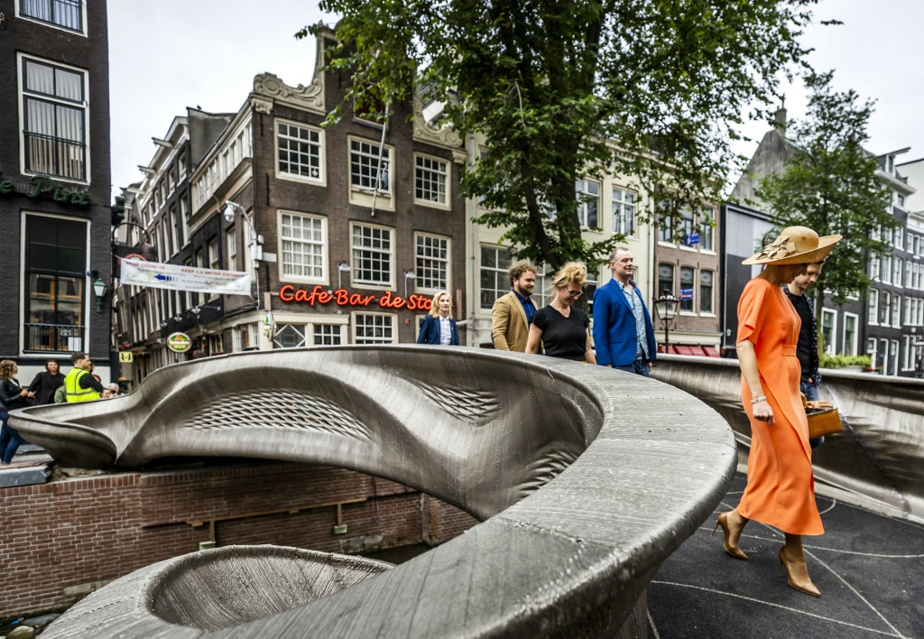
PHOTO ARCHIVES AGENCE FRANCE-PRESSE
Inauguration de la première passerelle d’acier imprimée en 3D, à Amsterdam, aux Pays-Bas, en juillet 2021
Du béton plus léger. Du bois qui résonne mieux. Des pièces de métal plus résistantes… L’impression 3D ne bouleverse pas seulement la médecine, elle transforme la fabrication des maisons, des avions, des ponts, des casques de vélo, etc. Les avantages ? Mettre fin au gaspillage de matériaux. Et créer rapidement – souvent à moindre coût – des formes beaucoup plus élaborées, sans moulage ni assemblage.
Bois
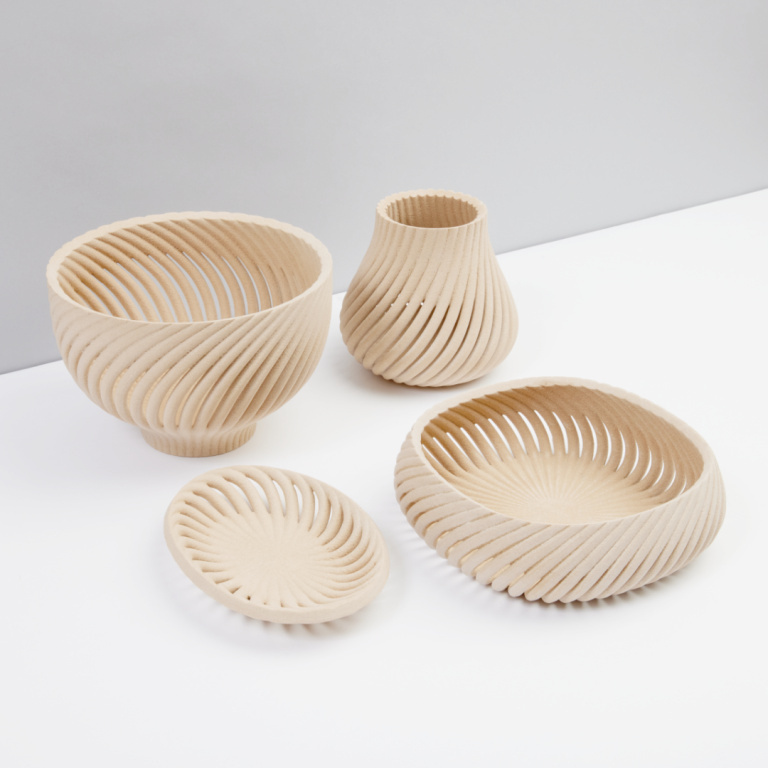
PHOTO TIRÉE DE FORUST.COM
La poussière de bois permet d’imprimer des objets qu'un artisan mettrait beaucoup de temps à créer.
Les tonnes de poussière de bois qui aboutissent au dépotoir peuvent servir à reproduire des bois rares, en imitant leur grain, couche par couche. On freinerait ainsi la déforestation et le trafic de bois précieux qui risquent de disparaître de la planète. Contrairement au contreplaqué, le bois imprimé peut être sablé en profondeur et emprunter des formes ouvragées qu’un ébéniste mettrait plusieurs semaines à ciseler. Ajuster la recette de fabrication permet d’améliorer ses propriétés, par exemple, en modulant la densité du « bois » pour parfaire la sonorité d’une guitare ou augmenter la solidité d’un meuble.
Béton
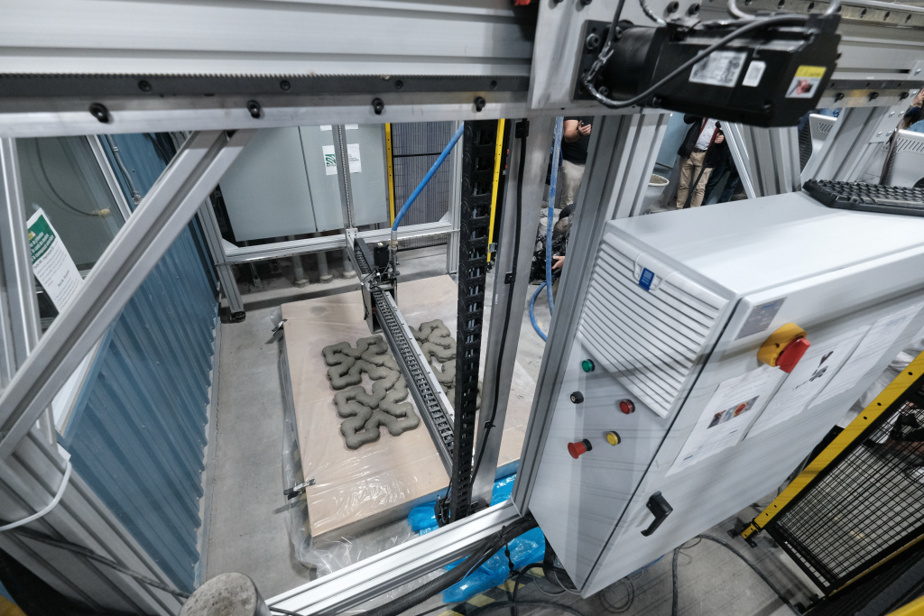
PHOTO MICHEL CARON, FOURNIE PAR L’UNIVERSITÉ DE SHERBROOKE
La gigantesque imprimante à béton conçue par l’équipe du professeur Ammar Yahia à l’Université de Sherbrooke. Elle requiert du béton optimisé.
Contrairement au béton traditionnel, le béton imprimé par couches successives n’a pas besoin de coffrage en bois, qu’on jette après usage et qui peut représenter 40 % des coûts d’un projet de construction. L’impression 3D permet en prime de créer plus facilement – et plus rapidement – des formes arrondies ou complexes. Certains mélanges produisent du béton plus léger ou beaucoup plus résistant aux désastres naturels. Au Canada, des chercheurs de l’Université de Sherbrooke ont été les premiers à concevoir une – imposante ! – imprimante 3D pour le béton. Elle servira entre autres à « réparer des ponts ou des barrages à des endroits plus difficilement accessibles », indique le site web de l’université. « On diminue le nombre de personnes présentes sur les chantiers, ce qui diminue par le fait même les risques de blessures », précise le même texte.
Bâtiments
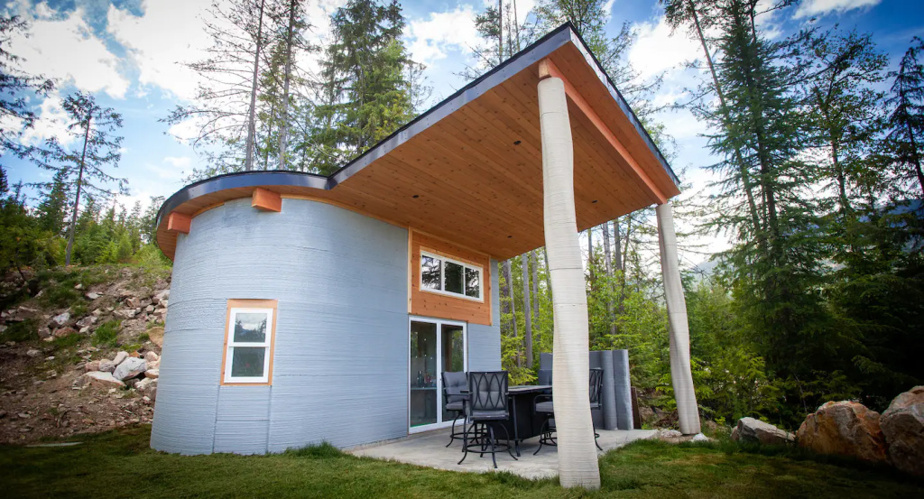
PHOTO TIRÉE DU SITE INTERNET D'AIRBNB
La toute première maison imprimée au Canada, située à Nelson, en Colombie-Britannique
Vue du ciel, la toute première maison imprimée au Canada a un peu la forme d’une coquille d’escargot. Située à Nelson, dans le sud de la Colombie-Britannique, elle est née en 11 jours avant d’être affichée sur la plateforme Airbnb, en juillet. L’organisme international World Housing, qui a financé sa construction, en a déjà érigé une dizaine dans le sud du Mexique, pour loger des familles sans abri. Imprimer des murs et des fondations est beaucoup plus rapide et abordable que de les fabriquer manuellement. Dès 2014, une entreprise de Shanghai a imprimé en une seule journée les murs de 10 petits édifices, en utilisant des déchets de construction et du ciment. L’été dernier, une société danoise a imprimé une école, au Malawi – une première mondiale.
Ponts
Depuis l’été dernier, les piétons européens peuvent fouler deux nouvelles passerelles imprimées en 3D. La première enjambe un canal du quartier Red Light, à Amsterdam. Faite d’acier – une première –, elle mesure 12 mètres de long et pèse près de 5000 kg. L’impression a duré six mois. La deuxième passerelle trône dans un parc voisin des jardins de la Biennale, à Venise. Plus de 50 blocs de béton ont permis de créer sa forme unique, qui s’étend sur 16 mètres. Ils ont la particularité de ne pas être renforcés avec de l’acier et d’être amovibles.
Équipement sportif
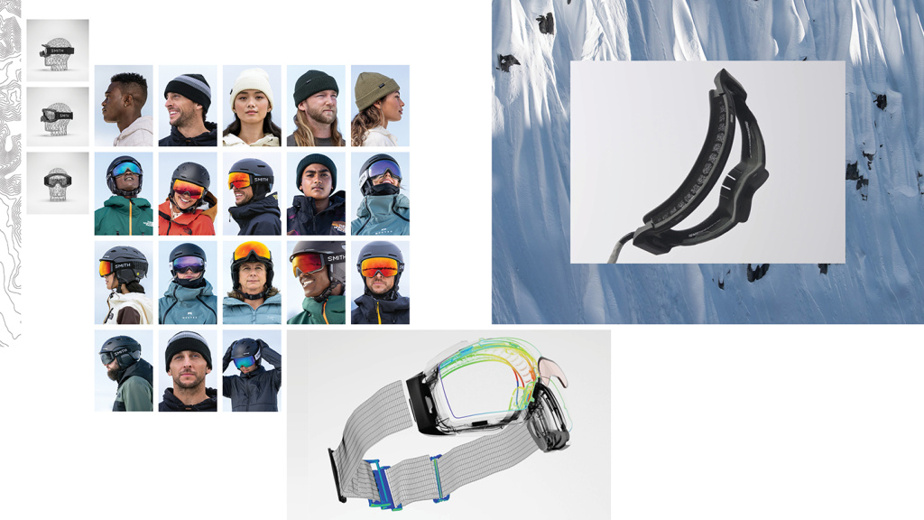
IMAGE TIRÉE DU SITE INTERNET DE SMITH OPTICS
Les lunettes de ski imprimées en 3D de Smith Optics
Depuis 2021, les joueurs de la Ligue nationale de hockey ont accès à des casques dotés d’une doublure imprimée en 3D. En forme de treillis, elle est plus légère que la mousse traditionnelle, amortit mieux les impacts et respire mieux. CCM espère en faire bénéficier les joueurs du dimanche, en scannant leur crâne en magasin. Le fabricant compte sur une firme montréalaise, Shapeshift 3D, pour transformer ce genre de numérisation en fichier d’impression. Depuis novembre dernier, l’entreprise américaine Smith Optics vend des lunettes de ski pareillement adaptées au visage de chaque client. Elles sont donc plus étanches tout en étant moins serrées. Le hic ? Leur coût : 510 $ CAN. En Angleterre, Herx commercialise quant à elle des casques de vélo sur mesure (environ 340 $ CAN chacun). L’entreprise parvient à en imprimer 6 en 36 heures.
Aliments
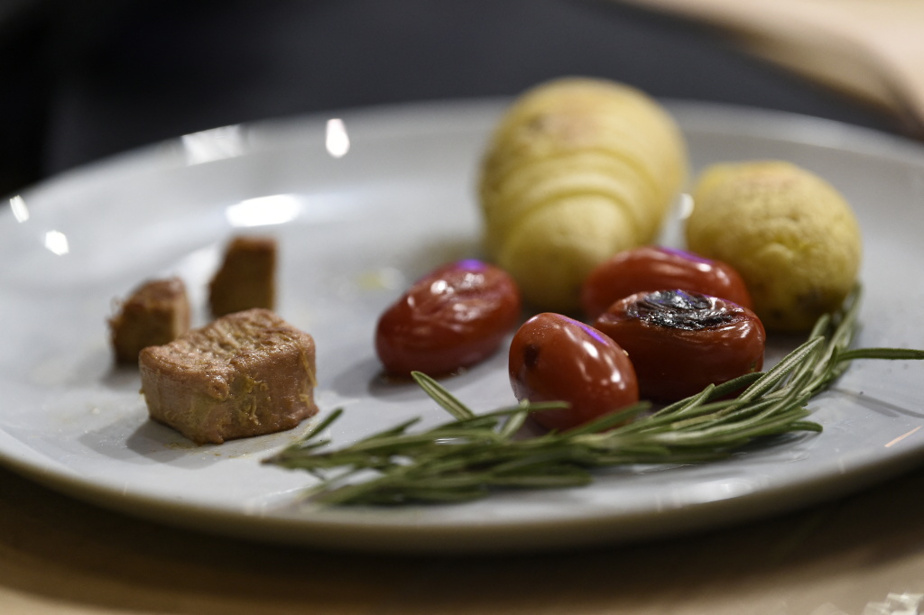
PHOTO JOSEP LAGO, ARCHIVES AGENCE FRANCE-PRESSE
Des morceaux de protéines végétales imitant le texture du bœuf imprimées par une imprimante 3D. Photo prise lors du salon Mobile World Congress à Barcelone, en Espagne, en juin 2021.
Une trentaine de restaurants européens servent déjà des « steaks » fabriqués en superposant des couches du soja, des pois, des betteraves, de la levure et du gras. Le processus permet d’imiter la texture fibreuse du bœuf, de l’agneau et du porc. D’après une journaliste du quotidien britannique The Guardian, la ressemblance s’avère « troublante ». L’entreprise israélienne qui a mis au point cette fausse viande, Redefine Meat, dit en imprimer environ 10 kg l’heure. Plus futuriste encore, et dans le même pays, Aleph Farms a imprimé des steaks de vraie viande à partir de cellules de vache cultivées en laboratoire. Ses pièces contiennent des muscles et du gras, et se révèlent apparemment juteuses. L’objectif : plaire aux carnivores en utilisant moins d’eau et de terres, et en produisant moins de méthane.
Chaussures
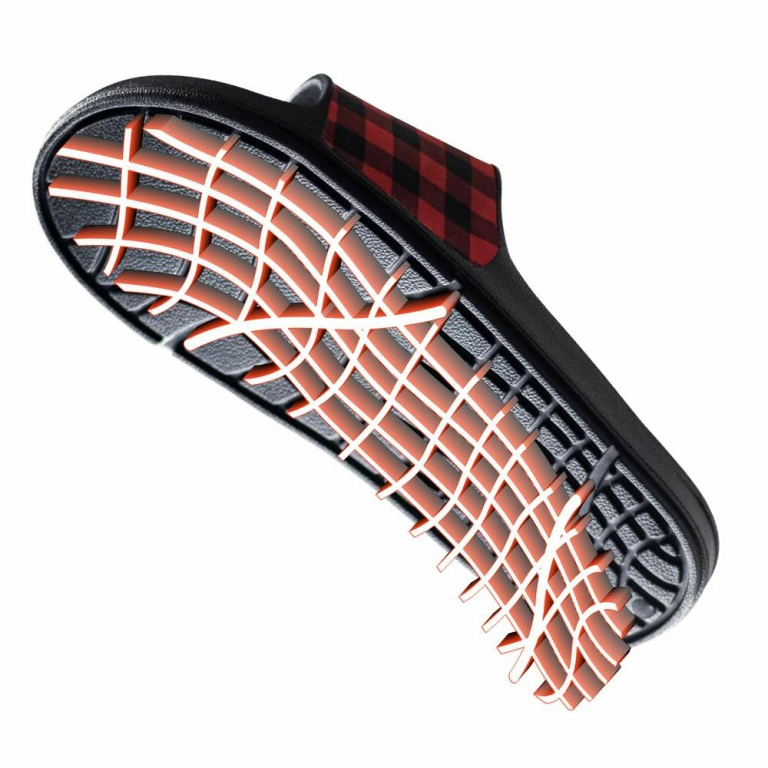
PHOTO TIRÉE DE FITMYFOOT.COM
Semelle imprimée en 3D
Dès 2018, Adidas a utilisé l’impression 3D pour produire des semelles en forme de treillis, censées atténuer l’impact. Reebok, New Balance et Nike impriment aussi les semelles de certains souliers. Au Canada, Wiivv imprime des semelles orthopédiques et des sandales de plastique sur mesure à partir d’une numérisation réalisée avec une application pour téléphone intelligent.
Santé
L’impression 3D sert de mille façons dans le secteur de la santé, entre autres pour produire des prothèses sur mesure, qui seraient autrement hors de prix. Le site ClinicalTrials.gov répertorie plusieurs dizaines d’essais cliniques mettant cette technologie à l’épreuve. Certaines entreprises impriment des moules en 3D et tentent d’y faire croître des cellules. Des chercheurs australiens affirment quant à eux qu’ils peuvent imprimer des os artificiels directement à l’intérieur du corps, au bon endroit, grâce à une sorte de céramique mêlée aux cellules des patients.
Métal
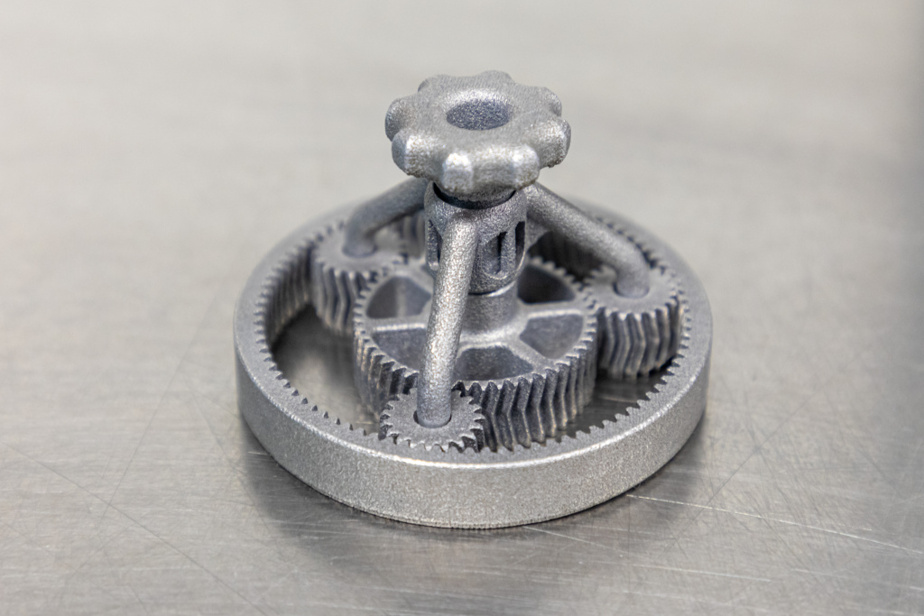
PHOTO PAUL DIONNE, COLLABORATION SPÉCIALE
Un système d’engrenage imprimé d’un seul bloc par le CRIQ
Imprimer des pièces métalliques permet de réaliser des prouesses, indique Lyne Dubois, vice-présidente du Centre de recherche industrielle du Québec d’Investissement Québec. Ses experts ont notamment fabriqué, pour Pratt & Whitney, une pièce de moteur d’aéronef dotée d’un vide au centre, pour l’alléger – ce qui aurait été impossible avec l’usinage traditionnel. Ils ont aussi imprimé d’un bloc un système d’engrenages, une tour jouet creusée d’un minuscule escalier et une pièce ondulée et ajourée comme de la dentelle. L’impression métallique prendra un « essor fulgurant », prédit la société d’État, qui aide les entreprises à viser les pièces à imprimer et la manière de le faire, et qui leur prête ses experts et ses équipements de pointe. « Elles doivent se réorganiser, apprendre à produire de façon différente, plaide Mme Dubois, parce que les consommateurs veulent des produits personnalisés. »
Fusée
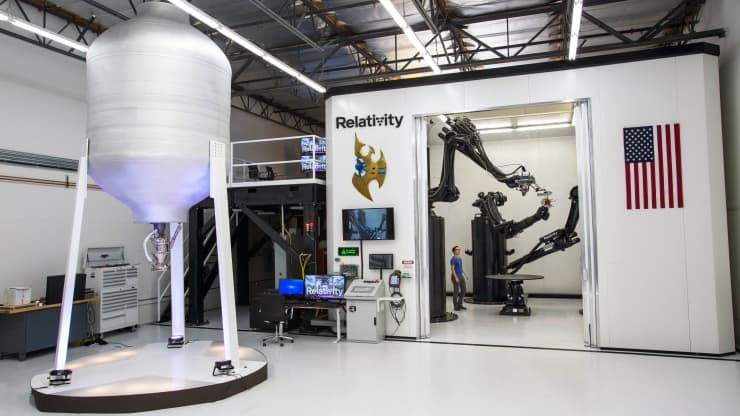
PHOTO TIRÉE DU SITE INTERNET DE RELATIVITY SPACE
Imprimante 3D de Relativity Space dans son usine de Los Angeles
Incroyable, mais vrai. Aux États-Unis, Relativity Space utilise des imprimantes gigantesques pour produire – en moins de deux mois – des fusées entières, du moteur à la carrosserie. L’entreprise a annoncé qu’elle en lancerait une de 30 mètres de haut en 2022, et en fabrique un nouveau modèle deux fois plus grand.
Révolution en 3D | La Presse - La Presse
Read More
No comments:
Post a Comment